Примеры решений
CO2 может использоваться в качестве хладагента в системах как с субкритическим, так и с транскритическим холодильным циклом.
В классическом субкритическом холодильном цикле, который традиционно используется, например, в большинстве холодильных систем на фреонах, весь диапазон рабочих температур и давлений находится ниже критической точки и выше тройной точки. Подобные системы на CO2 характеризуются простотой конструкции, ограниченным диапазоном рабочих температур и высоким давлением. Рабочее давление в субкритическом цикле находится обычно в диапазоне от 5,7 до 35 бар при соответствующей температуре от –55 до 0°C. Если испаритель оттаивается горячим газом, то значение рабочего давления увеличивается примерно на 10 бар.
Отличительная черта холодильных систем, использующих транскритический цикл охлаждения, отсутствие в конструкции конденсатора. Вместо него используется газоохладитель.
Это связано с тем, что отвод тепла от хладагента в транскритическом цикле происходит при температуре, превышающей критическую точку, так что конденсации при этом не происходит.
Так как фазовый переход не осуществляется, при прохождении через газоохладитель температура CO2 продолжает понижаться. Теплоемкость CO2 при охлаждении также изменяется. Разница температур между охлаждающей средой и CO2 в газоохладителе обычно составляет половину аналогичной разницы температур при конденсации хладагента. Чтобы добиться максимальной производительности, газоохладитель выполняют в виде теплообменника противоточного типа.
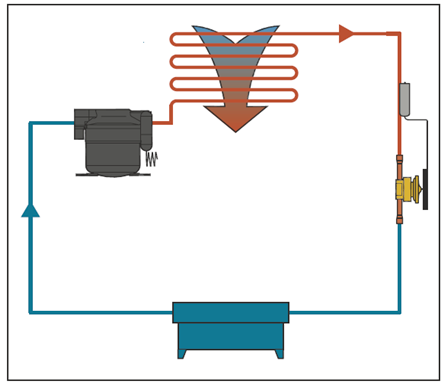
Схема простейшей холодильной установки, работающей в транскритическом режиме
Простейшая транскритическая установка состоит из компрессора, газоохладителя, испарителя и расширительного устройства (дроссельного отверстия или капиллярной трубки). В простейших установках нет регуляторов давления, и они, следовательно, работают при оптимальном высоком давлении и максимальной производительности при данных неизменных условиях работы. Другим вариантом является использование термостатического клапана для регулирования температуры охлаждения газа.
Одной из наиболее перспективных для применения в холодном климате является транскритическая бустерная система. Она более экономична в сравнении с системами, работающими на фреоне R404a, и в то же время отличается простотой конструкции.
Типичная транскритическая углекислотная бустерная система разделяется на три секции: высокого, среднего и низкого давления.
Секция высокого давления начинается с компрессора высокого давления, проходит через газоохладитель и теплообменник на всасывающей линии, а заканчивается клапаном регулирования высокого давления. Расчетное давление в этой секции, как правило, составляет от 90 до 120 бар.
Секция среднего давления начинается от расширительного клапана высокого давления, где поток разделяется на газ и жидкость в ресивере.
Газообразная фаза отводится во всасывающую линию компрессора высокого давления через перепускной клапан. Жидкая фаза подается к расширительным клапанам, где происходит ее расширение перед подачей в низкотемпературный и среднетемпературный испарители.
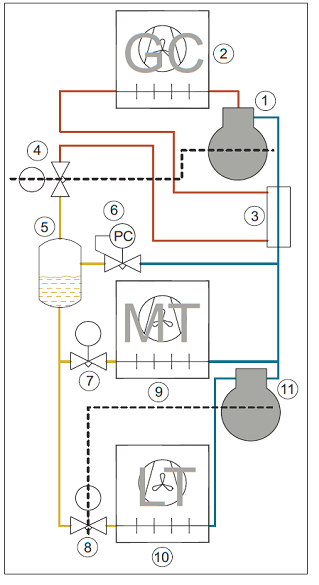
Схема транскритической бустерной системы с газовым перепускным клапаном
Газ из низкотемпературного испарителя сжимается в низкотемпературном компрессоре и смешивается с газами, поступающими из среднетемпературного испарителя и перепускной линии. Отсюда газ подается во всасывающую линию компрессора высокого давления и заполняет контур.
Расчетное давление в среднетемпературной секции обычно составляет 40–45 бар, а в низкотемпературной секции — 25 бар. При этом все чаще среднетемпературная и низкотемпературная секции рассчитываются на одинаковое давление.
Наиболее широко CO2 применяется в каскадных системах. В этом случае диапазон рабочих давлений позволяет использовать стандартное оборудование (компрессоры, регуляторы и клапаны), имеющееся в продаже.
Существуют различные виды каскадных холодильных систем на CO2: с непосредственным кипением, с насосной циркуляцией, с вторичным рассольным контуром, а также комбинации этих систем. Каскадная система состоит из двух изолированных холодильных контуров, сопряженных через каскадный теплообменник. В настоящее время распространение получили системы, в которых в качестве хладагента на низкотемпературной стороне используется CO2, а на высокотемпературной стороне — углеводороды, гидрофторуглероды (ГФУ) или аммиак. Высокотемпературного хладагента для каскадной системы требуется очень немного (значительно меньше по сравнению с обычной системой аналогичной производительности на том же хладагенте).
При этом рабочее давление CO2 в каскадных системах обычно невысокое — 40-45 бар, что соответствует температуре от +5 до +10°C, а разность температур у каскадного теплообменника — относительно низкая. Такие устройства особенно эффективны в условиях жаркого климата.
Поток CO2 в низкотемпературном контуре каскадной системы подается в испаритель либо благодаря разнице давлений, либо при помощи насоса.
Система с непосредственным кипением хладагента является более простой, так как в ней отсутствует насос и устройства контроля уровня жидкости. Такая система имеет также меньшую заправку хладагентом. Недостатком данной схемы является пониженная эффективность из-за более высокого перегрева на всасывании.
Поэтому такая схема обычно используется в небольших холодильных установках.
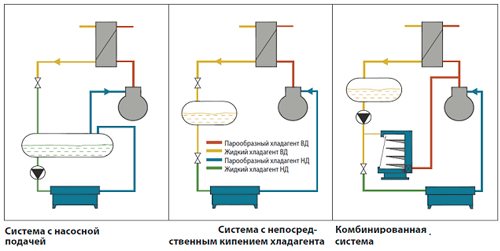
Различные виды компоновки каскадных систем
Каскадные системы на CO2 с насосной подачей отличаются высокой эффективностью, а небольшой размер трубопроводов, используемый как в низкотемпературных, так и в среднетемпературных применениях делает эти установки уникальными по сравнению с рассольными системами.
Лучшим применением схемы с насосной циркуляцией являются установки с относительно высокой производительностью. В установках с небольшой или переменной производительностью управление насосами затруднительно.